Preridotto: sperimentazione in corso
La riduzione delle emissioni di anidride carbonica (CO2) è oggi una delle priorità dell’industria siderurgica a livello mondiale. Uno dei metodi di decarbonizzazione più rapidi ed efficaci consiste nel passare da una produzione di acciaio basata su forni convertitori all’utilizzo di forni ad arco elettrico. Ciò comporterà inevitabilmente un aumento della domanda di rottame e la potenziale scarsità di questa materia prima.
Železiarne Podbrezová (ZP) adotta da decenni un ciclo di produzione dell’acciaio basato sul riciclo del rottame ferroso mediante forno ad arco elettrico. E, per essere pronta ad affrontare i diversi futuribili scenari, ha deciso di avviare delle sperimentazioni volte alla ricerca di un’alternativa al rottame e alla ghisa: il preridotto bricchettato o HBI (Hot Briquetted Iron), ovvero la forma compattata del preridotto.
Il preridotto, anche noto in Italia come DRI dalla sua traduzione in inglese (acronimo di Direct Reduced Iron), può essere ottenuto attraverso specifiche tecnologie che prevedono la riduzione del minerale di ferro utilizzando gas naturale o idrogeno. Ciò si traduce in una sostanziale riduzione delle emissioni di CO2 rispetto a quanto avviene durante la convenzionale produzione di ghisa negli altiforni.
“I bricchetti di preridotto hanno una composizione chimica simile alla ghisa. Non contengono elementi contaminanti quali rame e stagno. L’uso di HBI riduce così il contenuto di specie chimiche indesiderate nell’acciaio“, ha spiegato l’Ing. Stanislav Turňa, tecnologo di processo dell’acciaieria. “I bricchetti contengono ferro per oltre l’80%. Possono dunque parzialmente sostituire i rottami ferrosi”.
E quali sono gli impatti sul processo fusorio? “Il preridotto viene aggiunto al rottame di acciaio e quindi fuso nel forno ad arco elettrico. All’aumentare del contenuto di preridotto, si allunga il tempo necessario per lo smelting. Questo consumerà poi più elettricità, ossigeno e altre materie prime. A causa del maggior contenuto di ossidi e di carbonio, le procedure da adottarsi nella gestione del forno sono diverse in presenza di un elevato contenuto di preridotto rispetto al processo basato sul rottame. Se grandi quantità di preridotto fossero alimentate al forno, sarebbe necessaria la creazione di nuovi programmi di fusione o l’installazione di nuovi tipi di bruciatori, modificando le aggiunte di altri materiali quali calce o dolomite”.
Il preridotto come alternativa al rottame ferroso
Nel mese di febbraio il preridotto è stato utilizzato presso la nostra acciaieria. Finora si è trattato solo di una sperimentazione: “il preridotto bricchettato fu provato nella nostra acciaieria per la prima volta nel 2005. A quel tempo, producevamo acciai speciali per l’industria automobilistica“, ha affermato Turňa, aggiungendo che il preridotto non è poi più stato utilizzato dal 2011. Ora, dopo più di dieci anni, l’acciaieria ha concluso un nuovo ciclo di test con l’HBI.
“Partiamo dall’ipotesi che in futuro potrebbe esserci una carenza di rottame. Come accennato, dobbiamo cercare soluzioni alternative. Inoltre, a causa delle emissioni, molte acciaierie stanno abbandonando l’utilizzo di altiforni, cosa che ridurrà la disponibilità di ghisa. Questa materia prima fa parte della carica del forno elettrico ad arco. Ecco perché la nostra acciaieria ha avviato delle sperimentazioni con il preridotto“.
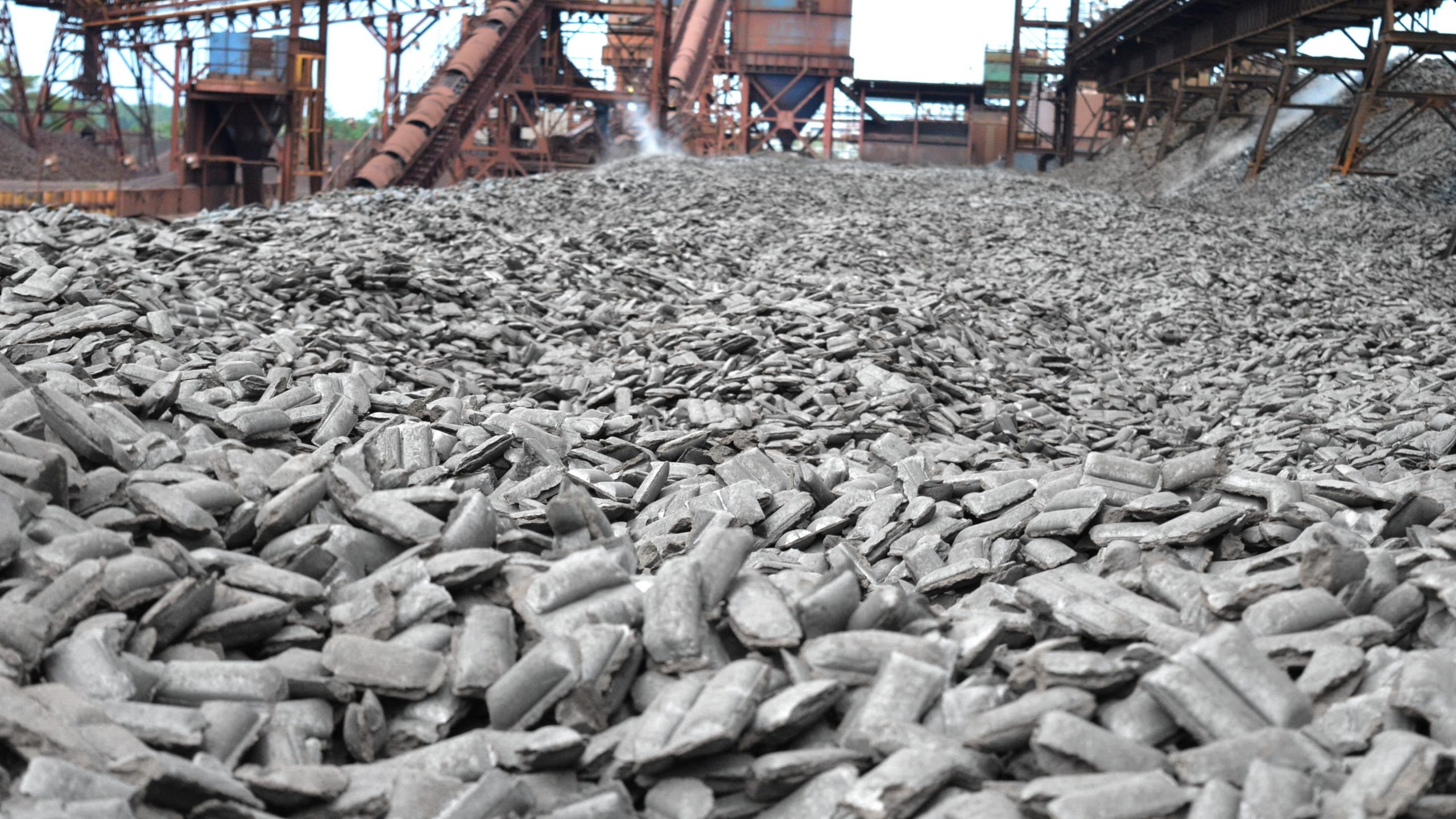
Una complessa ottimizzazione del processo
ZP ha già completato le prime prove di fusione e i risultati sono attualmente in fase di analisi. “Abbiamo realizzato 60 colate. Siamo passati sistematicamente da quantità minori a quantità maggiori. Gradualmente abbiamo evidenziato delle problematiche, ottimizzato il processo e ricercato delle soluzioni per rendere lo smelting più efficiente. Abbiamo anche tenuto traccia dei costi di produzione. Ad oggi, abbiamo usato quasi 400 tonnellate di preridotto nei nostri test“, ha affermato Turňa.
Il preridotto potrebbe essere in grado di sostituire il rottame in futuro. Tuttavia “dobbiamo renderci conto che tale opzione non è la soluzione più economica e la sostituzione completa dei rottami con l’HBI non è attualmente considerata“, ha risposto il tecnologo.
L’utilizzo del preridotto comporta anche una novità per gli stessi operatori; “oltre al regolare monitoraggio dei parametri di processo, gli operatori devono anche verificare se il preridotto sia fuso o se siano presenti dei residui a contatto delle pareti o sul fondo del forno. L’intero processo è una novità. La maggior parte di noi è entrata in contatto con il preridotto per la prima volta“, ha detto il tecnologo, indicando i colleghi che hanno diligentemente monitorato il processo di fusione durante i test.
La nostra acciaieria ha condotto i test utilizzando cinque, sette e dieci tonnellate di preridotto bricchettato per colata. I tecnologi e il personale dell’acciaieria stanno analizzando i dati raccolti, cercando di stabilire i parametri ottimali del processo produttivo.
Le dinamiche future dell’industria siderurgica sono incerte, ma ZP, con questa campagna sperimentale e le altre attività di ricerca attualmente in corso, mira ad essere pronta ad affrontare qualsiasi circostanza; restando all’avanguardia nello sviluppo tecnico per rimanere efficiente e competitiva in ogni possibile scenario.
Articolo scritto da:

Luca Orefici
Green Manager
Per ulteriori informazioni, dettagli o richieste, non esitate a contattarci tramite marketing@pipex.it.
Non perdere le nostre notizie e iniziative, leggi il nostro BLOG e iscriviti alla nostra Newsletter